
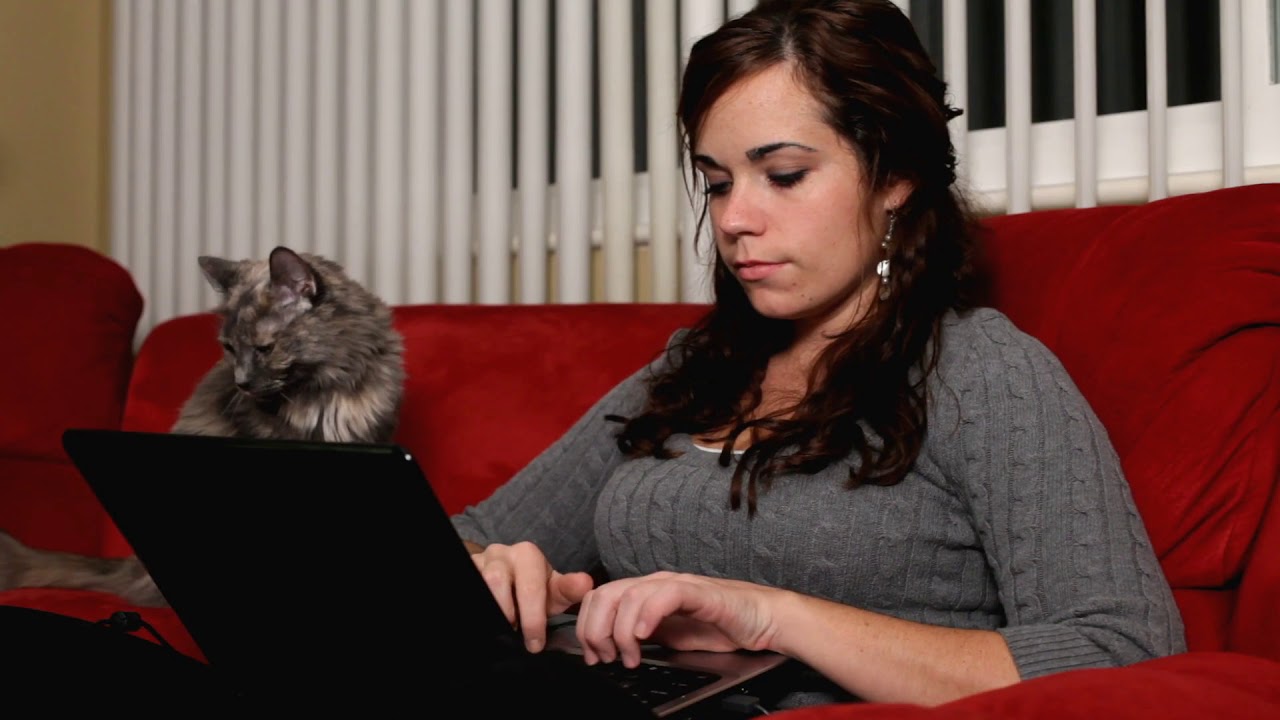
“It simply can’t work unless you have a closed loop for the raw materials,” he says. These days he talks about his mission with a breathless excitement coupled with the precision of an engineer, sometimes pausing in the middle of a thought to start over as he explains his vision for the future of battery production. Straubel started Redwood while still working at Tesla (he left in 2019) he wanted, as he puts it, to create a sustainable battery materials company. He began to think of ways to lower the cost of batteries and help reduce the carbon emissions associated with making them. But even as Tesla was transforming the way electric cars were manufactured and sold, Straubel was worried about how overwhelming the need for more battery materials would become. Redwood Materials was founded by JB Straubel, who as Tesla’s chief technical officer during the early 2010s led many of the company’s battery breakthroughs, including the beginnings of its network of charging stations. Redwood has big plans and plenty of construction ahead. But the two other major buildings still looked far from completion-one was missing walls, and the other was only a foundation. By 2025, Redwood projects, its facility will produce enough of them to make batteries for more than a million EVs every year.ĭown the hill from the trailers, the building for copper foil production was the furthest along, with a roof and walls a machine for making the foil was tucked away in the corner. These components account for over half the cost of battery cells. When construction is finished, the Redwood site will produce two major products: the copper foil for anodes and a mixture of lithium, nickel, and cobalt known as cathode active material.

Several massive buildings were under construction, and engineers and construction workers in safety vests and hard hats hurried around the site, ducking between temporary trailers serving as makeshift offices, labs, and meeting rooms. Later, I’d spot a coyote skittering across the parking lot.īut down the dirt road at the site, the Old West vibes quickly fell away, replaced by a sense of urgency radiating from nearly everyone there. On the way to Redwood’s factory, I saw tumbleweeds leap across the highway, and some of the area’s wild horses idled on a hillside. It’s sending the foil to the battery maker Panasonic to use in the Nevada Gigafactory, which produces battery cells for Tesla vehicles less than five miles away. When I visited in September, Redwood was preparing to ship its first product, a small sample of copper foil used in battery anodes. But thanks to these advances, it could account for a significant fraction of supply in the coming decades.

Recycling can’t address material shortages alone, because demand for the metals outstrips the amount circulating in batteries used today.

New advances in the recycling process for lithium-ion batteries are transforming the industry, allowing recyclers to separate and recover enough of these valuable metals to make the process economical. And it could really take off after that, as the first generation of electric cars heads for the junkyards. That number is expected to top 1.6 million metric tons by 2030, according to the consulting firm Circular Energy Storage. Globally, there was over 600,000 metric tons of recyclable lithium-ion batteries and related manufacturing scrap in 2021. Recycling could represent a major new source of raw materials.
